Special Performance Requirements for Wind Power Equipment Wiring Harnesses
Wire harnesses play a vital role in wind power generation equipment. Due to its complex and changeable operating environment, it faces many challenges such as high temperature, cold, humidity, salt spray, strong wind and electromagnetic interference, so there is a strict demand for the special performance of the wire harness.

Table of contents
I. Electrical Performance
The wiring harnesses of wind power equipment have stringent requirements in terms of electrical performance to ensure efficient and stable energy transmission and signal control. Since wind power systems typically operate in high-voltage, high-current, long-distance transmission, and strong electromagnetic interference environments, the electrical performance of the wiring harnesses directly impacts the reliability and efficiency of the entire system.
1. High Voltage/Current Carrying Capacity
The output voltage of wind turbines varies widely, typically ranging from 690V to 35kV (depending on the model and grid voltage level). Therefore, the wiring harness must meet high-voltage insulation requirements:
• Insulation Materials: Cross-linked polyethylene (XLPE), ethylene propylene rubber (EPR), or silicone rubber with a dielectric strength of ≥20 kV/mm.
• Conductor Cross-Sectional Area: For high-current transmission (e.g., from the tower to the converter), copper conductors with a cross-sectional area of ≥50 mm² are required to reduce resistive heat loss (I²R).
• Voltage Withstand Test: The harness must pass power-frequency withstand voltage tests (e.g., 3.5 kV for 5 minutes without breakdown).

2. Low Capacitance and Impedance Matching
Long-distance cables (e.g., from the nacelle to the base control cabinet) must control distributed parameters to avoid signal attenuation and reflection:
• Distributed Capacitance: ≤100 pF/m to minimize high-frequency signal distortion (e.g., PWM signals for pitch control).
• Impedance Matching: Communication lines (e.g., CAN bus, Ethernet) must maintain stable characteristic impedance (e.g., 120Ω ±10%) to prevent signal reflection.

3. Electromagnetic Interference (EMI) Resistance
Wind power environments feature strong electromagnetic interference (from converters, inverters, etc.), requiring wiring harnesses with excellent shielding performance:
• Shielding Structure: Copper braiding (≥85% coverage) or aluminum foil composite shielding layers, with shielding effectiveness ≥90 dB (1 MHz–1 GHz).
• Twisted Pair Design: Differential signal lines (e.g., RS485, CAN) use twisted pairs to reduce common-mode interference.
• Grounding Method: Single-point grounding of the shielding layer to avoid ground loops.

4. Partial Discharge and Corona Resistance
High-voltage harnesses (e.g., ≥10 kV) must prevent corona discharge to avoid insulation aging:
• Semiconducting Shielding Layer: A conductive layer between the conductor and insulation to evenly distribute the electric field.
• Material Selection: Corona-resistant materials (e.g., XLPE with nano-fillers).

5. Low-Loss Transmission
To minimize energy loss, the harness must exhibit low resistance and low dielectric loss:
• Conductor Resistance: DC resistance ≤0.2 Ω/km at 20°C (per IEC 60228).
• Dielectric Loss Tangent (tanδ): ≤0.001 (tested at 1 kHz to prevent high-frequency losses).
6. Transient Overvoltage Resistance
Wind power systems may experience lightning strikes or switching surges, requiring harnesses with high surge tolerance:
• Lightning Strike Resistance: Withstand at least 10 kA (8/20 μs waveform) per IEC 61400-24.
• Surge Protection: TVS diodes or varistors installed on critical signal lines (e.g., sensor lines).

Summary
The electrical performance of wind power wiring harnesses directly affects system stability, efficiency, and lifespan. Design considerations must prioritize high-voltage tolerance, low loss, EMI resistance, and impedance matching, adhering strictly to IEC, UL, and other relevant standards to ensure long-term reliability in complex electromagnetic and harsh operating conditions.
II. Mechanical Performance
Wind turbine wiring harnesses operate under complex mechanical stress conditions for extended periods, including high-frequency vibrations, bending, tension, torsion, and external impacts. To ensure stable operation throughout their 20+ year service life, these harnesses must meet stringent mechanical performance requirements.
1. Vibration Resistance and Fatigue Endurance
During turbine operation, blade rotation, gearbox vibrations, and tower oscillations subject wiring harnesses to continuous mechanical stress, necessitating exceptional vibration resistance:
• Vibration Testing Standards: Compliance with IEC 61400-2 (Vibration Testing Specification for Wind Turbines), requiring passage of 10-2000Hz random vibration tests (5Grms acceleration, ≥100 hours duration).
• Bending Fatigue Resistance: Conductors must use ultra-fine stranded tin-plated copper wires (e.g., 0.1mm single wire diameter) with high-elasticity sheathing (e.g., TPU or silicone) to ensure ≥10 million bending cycles without failure.
• Mounting Methods: Harnesses require anti-loosening clips or cable ties with vibration-damping pads to prevent connector detachment from vibrations.

2. Tensile and Compression Strength
• Vertical Wiring Tension: Tower-installed harnesses must withstand self-weight plus additional wind-induced tension, requiring tensile strength ≥500N (reinforced with aramid fibers or steel wire armoring).
• Crush Resistance: Sheathing must pass ISO 6722 compression tests (500N pressure, ≤30% deformation rate) to prevent damage during installation/maintenance.

3. Torsion and Bend Resistance
• Yaw System Compatibility: Harnesses must endure ±720° torsion (per IEC 60811-2-3) during nacelle rotation, with ≤5% conductor resistance variation.
• Minimum Bend Radius: Dynamic routing (e.g., pitch systems) requires ≥5× cable diameter; static routing ≥3×, to prevent insulation damage.

4. Abrasion and Impact Resistance
• Abrasion Testing: Compliance with EN 50396 (≥500 wire brush cycles) without sheath damage.
• Impact Protection: Exposed harnesses require polyurethane armor or stainless steel braiding to withstand hail/stone impacts.
5. Flexibility and Bendability
• High-Flex Design: Moving components (e.g., pitch motor connections) need ultra-flexible cables (silicone insulation + non-woven wrapping) for confined-space routing.
• Low-Temperature Flexibility: Must remain bendable at -40°C (per IEC 60811-1-4) without sheath cracking.
6. Kink and Tangle Prevention
• Anti-Kink Structures: Critical areas (e.g., terminal entries) use spiral sleeves or spring guards to prevent conductor breakage from repeated bending.
• Tangle Reduction: Long harnesses employ modular raceways for organized routing.
Key Mechanical Performance Comparison (Example)
Performance Requirement | Test Standard | Typical Specification | Solution |
Vibration Resistance | IEC 61400-2 | 5Grms, 100hrs failure-free | High-elasticity TPU sheath + damping mounts |
Tensile Strength | IEC 60228-6 | ≥500N no breakage | Aramid fiber reinforcement |
Torsion Resistance | IEC 60811-2-3 | ±720° no damage | Spiral shielding structure |
Abrasion Resistance | EN 50396 | ≥500 cycles no wear | Polyurethane outer sheath |

Summary
The mechanical performance of wind turbine wiring harnesses critically impacts long-term reliability, requiring focused solutions for vibration, tension, torsion, and abrasion. Through high-flex conductors, reinforced sheathing, and anti-loosening fixtures, harnesses maintain stable operation under extreme mechanical stresses, meeting 20+ year durability requirements.
III. Environmental Endurance
Wind power equipment typically operates under extreme environmental conditions, including offshore salt spray, desert heat, polar cold, and high-altitude UV exposure. As critical components for power transmission and signal control, wiring harnesses must demonstrate superior environmental endurance to ensure long-term system stability. The following details the environmental endurance requirements from multiple dimensions:
1. Extreme Temperature Resistance
Wind turbines operate across a wide temperature range (-40°C in Arctic regions to +60°C in deserts), requiring harness materials to adapt accordingly:
• Low-Temperature Performance:
- Materials must remain flexible at -40°C (per IEC 60811-1-4)
- No cracking or brittleness in sheathing
- Conductor resistance variation ≤5% (referencing IEC 60228)
• High-Temperature Performance:
- Continuous operation at +90°C, short-term tolerance to +125°C (e.g., nacelle hotspots)
- Materials must pass thermal aging tests (IEC 60216, 2000hrs @105°C)
- Insulation resistance ≥100MΩ·km at high temperatures
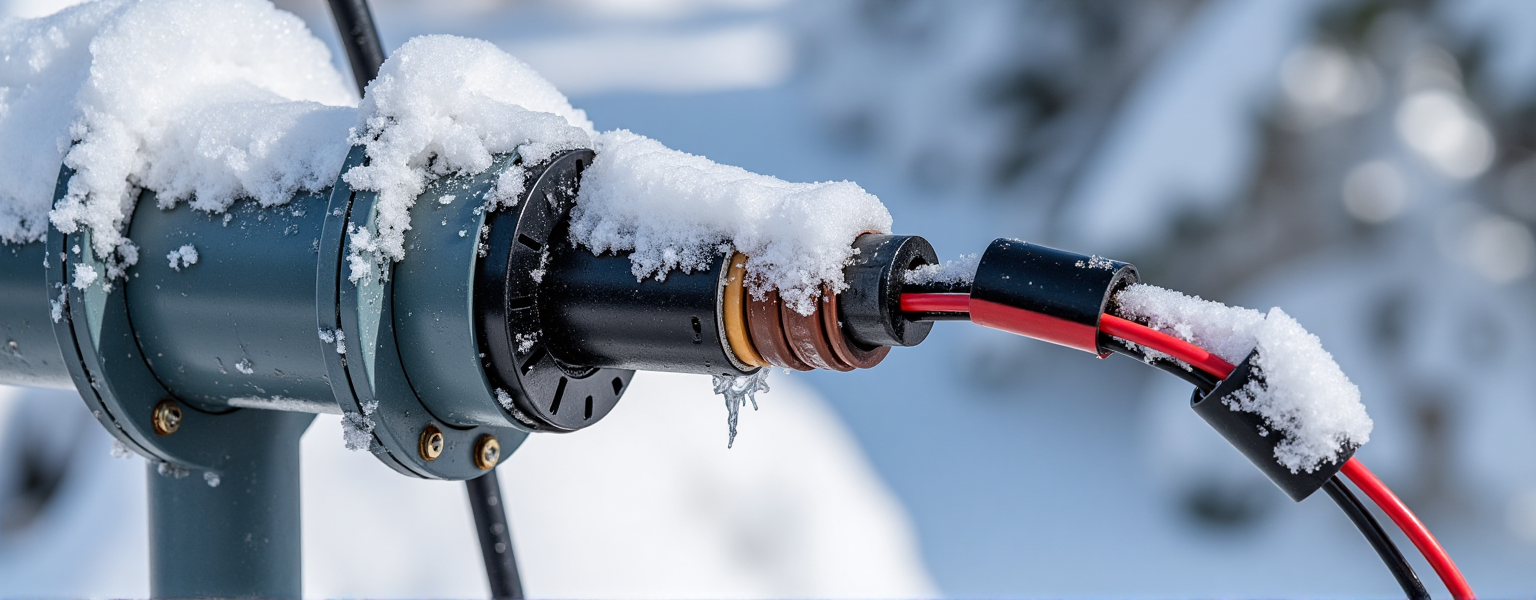
2. Moisture & Salt Spray Corrosion Resistance
Offshore and coastal environments present severe challenges:
Requirement | Test Standard | Specification | Solution |
Waterproofing | IEC 60529 | IP67 rating | Silicone gaskets + heat-shrink tubing |
Salt spray resistance | ISO 9227 | 1000hrs no corrosion | Tin-plated copper + anti-corrosion coating |
Moisture resistance | IEC 60068-2-78 | 56-day damp heat test passed | Moisture-resistant XLPE insulation |

3. UV & Ozone Aging Resistance
Exposed harnesses must withstand prolonged UV radiation and ozone exposure:
• UV Aging Test:
- Passes ISO 4892-3 (3000hrs UV exposure)
- ≥70% tensile strength retention in sheathing
- Color change ΔE≤3 (gray scale)
• Ozone Resistance:
- Passes IEC 60811-2-1 (0.5ppm ozone, 72hrs)
- No surface cracking
- Particularly critical for high-altitude installations (elevated ozone levels)
4. Chemical Corrosion Resistance
Various chemicals at wind farms may degrade harnesses:
• Oil Resistance:
- Passes ISO 1817 (70hrs immersion in IRM 902 oil)
- ≤50% volume expansion
- Recommended materials: NBR or CR rubber
• Acid/Alkali Resistance:
- Passes IEC 60754-1/2
- No corrosion within pH2-pH12 range
- Suitable for wind farms near chemical plants

5. Biological Degradation Resistance
Biological factors in special environments:
• Rodent Protection:
- Capsaicin-based repellents
- Metal braiding as physical barrier
• Mold Resistance:
- Passes IEC 60068-2-10 (28-day mold culture)
- Growth Class 0 (no growth)
- Essential for tropical rainforest climates
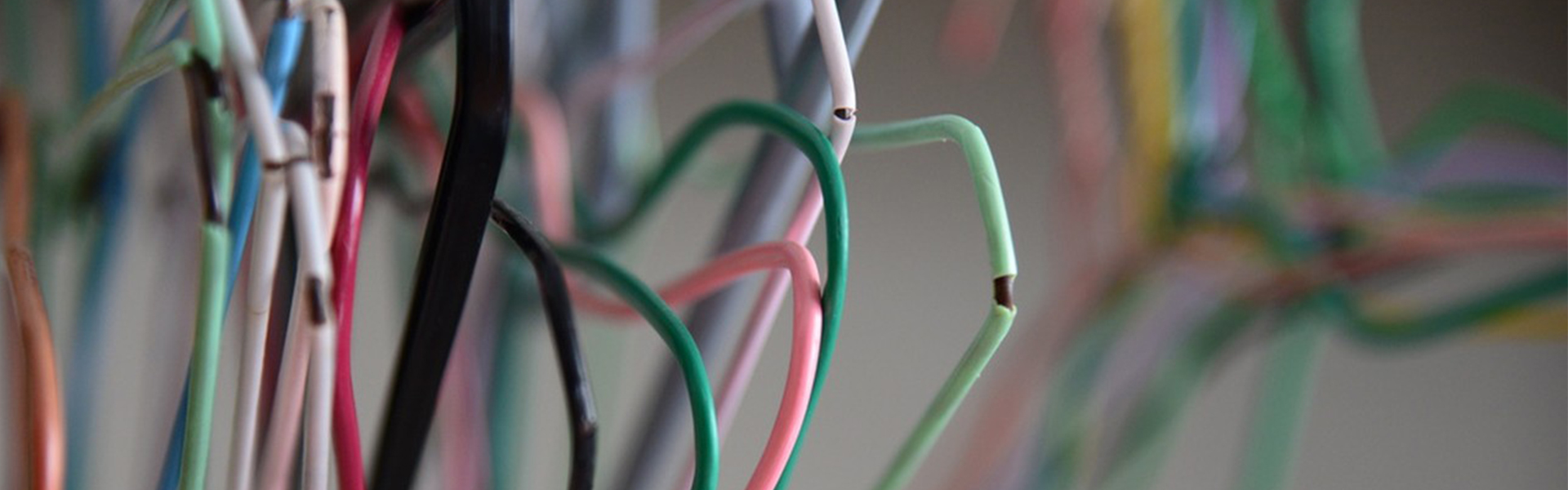
6. High-Altitude Adaptability
Special requirements for installations above 2000m:
• Corona Discharge Protection:
- Voltage rating increases 1% per 100m elevation
- Semiconductor shielding layers required
• Low-Temperature/Low-Pressure Performance:
- Passes IEC 60068-2-13 (50kPa low-pressure test)
- Insulation materials must avoid air gap formation

Key Environmental Test Examples
Test Item | Standard | Pass Criteria | Failure Mode |
Thermal cycling | IEC 60068-2-14 | 20 cycles no cracking | Sheath embrittlement |
Salt spray | ISO 9227 | 1000hrs no corrosion | Conductor oxidation |
UV aging | ISO 4892-3 | 3000hrs performance maintained | Color fading/surface chalking |
Oil resistance | ISO 1817 | ≤50% volume change | Material swelling |
Summary
The environmental endurance of wind power harnesses directly determines reliability under harsh conditions. Design considerations must address:
- Wide temperature operation (-40°C to +125°C)
- High protection ratings (≥IP67)
- Long-term weatherability (20+ year lifespan)
- Special environment adaptability (high-altitude, offshore, etc.)
These requirements demand rigorous testing per IEC/ISO standards to ensure wind power system longevity.
IV. Chemical and Biological Stability
Wind turbine wiring harnesses are exposed to various chemical substances and biological factors during long-term operation. Their chemical and biological stability directly affects equipment service life and reliability. This section provides a detailed analysis of special performance requirements under chemical corrosion and biological erosion conditions.
1. Chemical Corrosion Resistance
1.1 Oil Resistance
Potential oil leakage from lubrication systems requires excellent oil resistance:
- Test Standard: ISO 1817 (Liquid Immersion Test)
- Performance Requirements:
- After 70 hours immersion in IRM 902 standard oil
- Volume expansion ≤50%
- Tensile strength retention ≥70%
- Recommended Materials:
- Nitrile rubber (NBR)
- Chloroprene rubber (CR)
- Specially formulated polyurethane (TPU)
1.2 Acid/Alkali Resistance
Potential industrial pollution or natural acidic/alkaline environments:
- Test Conditions:
- pH2-pH12 range
- Temperature 23±2℃
- 168-hour immersion
- Acceptance Criteria:
- No significant visual changes
- Insulation resistance ≥100MΩ·km
- Dielectric loss tangent variation ≤20%
1.3 Solvent Resistance
Maintenance chemicals and solvents exposure:
Solvent Type | Test Standard | Acceptance Criteria |
---|---|---|
Ethanol | IEC 60811-2-1 | No swelling after 24h immersion |
Acetone | ISO 1817 | Volume change ≤30% |
Xylene | ASTM D543 | Mechanical property retention ≥80% |

2. Biological Erosion Resistance
2.1 Rodent Protection
Rodent bite prevention measures:
- Protection Methods:
- Physical: Stainless steel braiding (≥90% coverage)
- Chemical: Capsaicin additives (0.1-0.5% concentration)
- Structural: Armored sheath (thickness ≥0.5mm)
- Test Methods:
- UL 94 vertical burn test (including flame retardancy evaluation)
- Field exposure test (6 months)
2.2 Mold Resistance
Humid environment protection:
- Test Standard: IEC 60068-2-10
- Requirements:
- Mold growth Class 0 after 28-day culture
- Surface resistance variation ≤10%
- Solutions:
- Organotin-based fungicides
- Inorganic antimicrobial materials (e.g., nano-silver)
- Special surface treatment (micron-level roughness)
2.3 Insect Protection
Region-specific insect prevention:
- Special Requirements:
- Sheath surface roughness Ra≤0.8μm
- Avoid fluorescent materials that attract insects
- Possible DEET-based repellents

3. Material Stability Requirements
3.1 Long-Term Chemical Stability
- Aging Tests:
- Thermal: IEC 60216 (105℃×2000h)
- Damp heat: IEC 60068-2-78 (40℃,93%RH×56d)
- Performance Retention:
- Elongation at break ≥70% of initial value
- Volume resistivity ≥1×10^14Ω·cm
3.2 Material Compatibility
Inter-material interaction considerations:
- Key Focus Areas:
- Insulation-conductor compatibility
- Material migration at sheath interfaces
- Chemical reactions with sealing components
- Test Methods:
- High-temperature contact test (70℃×168h)
- Fluid compatibility test (ASTM D471)

4. Special Environmental Adaptability
4.1 Offshore Wind Requirements
- Corrosion Protection:
- Triple protection: Plating+coating+sealing
- Cathodic protection compatibility
- Test Standards:
- ISO 9227 salt spray test (3000h)
- IEC 60068-2-52 cyclic corrosion test
4.2 Desert Region Requirements
- Sand Erosion Resistance:
- Surface hardness ≥Shore D 60
- Abrasion test: ISO 4649 (wear volume ≤100mm³)
Key Performance Comparison
Performance Category | Test Standard | Acceptance Criteria | Typical Failure Mode |
---|---|---|---|
Oil resistance | ISO 1817 | Volume change ≤50% | Material softening |
Mold resistance | IEC 60068-2-10 | Growth Class 0 | Surface resistance degradation |
Rodent resistance | UL 94 | No penetration damage | Insulation damage |
Material compatibility | ASTM D471 | Property change ≤15% | Material embrittlement |
Summary
Chemical and biological stability are critical for long-term reliable operation of wind turbine harnesses, requiring focus on:
- Comprehensive protection design: Targeted solutions for different chemical/biological threats
- Advanced material science: Novel composite and polymer materials
- Rigorous testing: Accelerated aging simulating 20-year service
- Environmental adaptability: Location-specific protection strategies
We recommend conducting thorough chemical/biological risk assessments during design, selecting proven materials/protection solutions, and establishing periodic inspection/maintenance protocols to ensure stable performance throughout the product lifecycle.
No comments to show.
Leave a Comment