How to Select the Right Robot Cable Harness: 5 Key Factors
In modern industrial automation, robot cable harnesses serve as the “nervous system” and are critically important, as their performance directly affects the stability, safety, and service life of the entire robotic system.
With increasingly complex application scenarios for industrial robots—ranging from precision electronic assembly to heavy-duty automotive welding, from cleanroom medical operations to outdoor engineering work—the requirements for cable harnesses have also shown a trend toward diversification and specialization.
Selecting the right robot cable harness is far from a simple matter of specification matching; it requires a systematic engineering approach that comprehensively considers five key factors: electrical performance, mechanical characteristics, environmental adaptability, connector design, and standards certification.

Table of contents
I. Electrical Performance Factors
Electrical performance is the core consideration in robot cable harness selection, directly affecting signal transmission quality, system stability and safety. It mainly includes the following key indicators:

1. Current Carrying Capacity
(1) Conductor Cross-Sectional Area Selection
Select appropriate wire gauge based on load current to avoid overheating or excessive voltage drop. Common conductor cross-sectional area vs current rating reference table:
Conductor CSA (mm²) | Allowable Current (A) | Typical Applications |
0.5 | 3-5 | Sensor signal lines |
1.0 | 8-10 | I/O control lines |
1.5 | 12-15 | Servo motor power supply |
2.5 | 18-25 | Main power lines |
4.0 | 25-35 | High-power drivers |
▶ Note: Actual current rating should be adjusted considering ambient temperature, wiring method (such as bundling heat dissipation conditions) and other factors
(2) Voltage Rating Matching
Insulation material requirements for different working voltages:
Voltage Rating (V) | Min Insulation Thickness (mm) | Typical Test Voltage (V) |
≤60 | 0.4 | 500 |
300 | 0.6 | 2000 |
600 | 1.0 | 2500 |
1000 | 1.4 | 3500 |
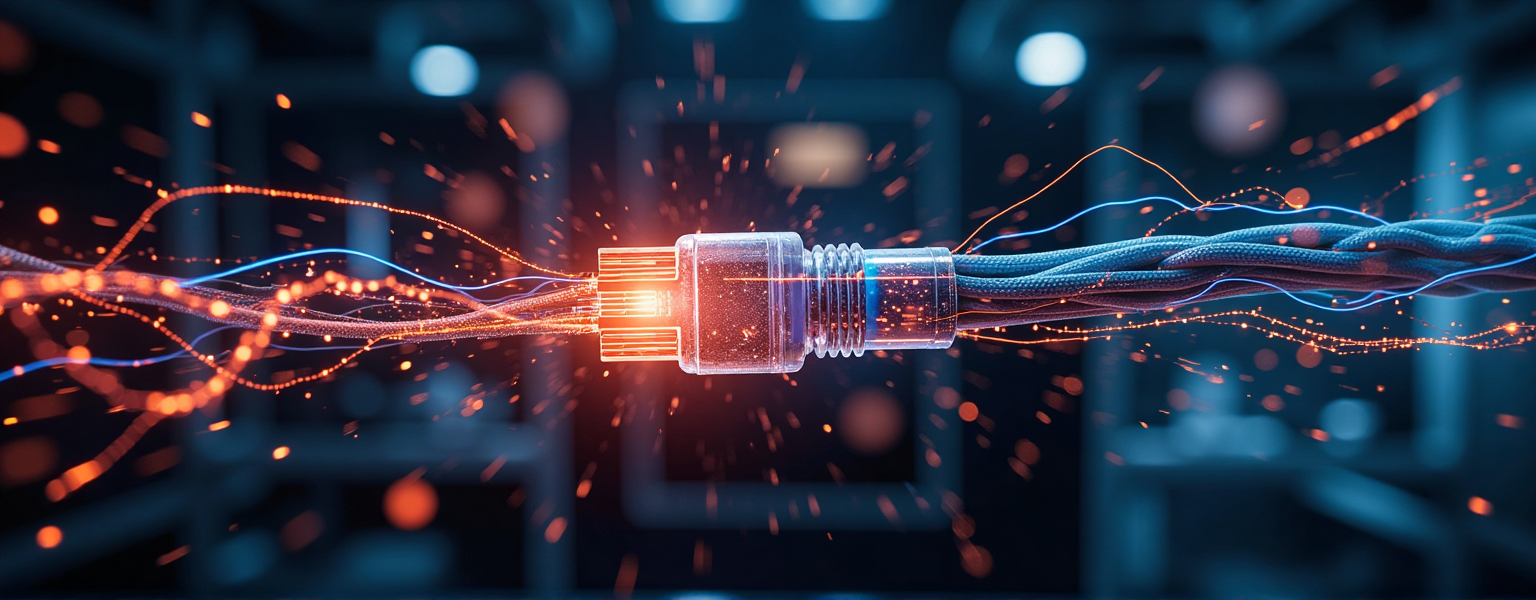
2. Signal Transmission Characteristics
(1) Cable Type Selection Comparison
Cable Type | Max Frequency | Attenuation Coefficient (dB/m) | Typical Applications |
Unshielded single wire | 1MHz | 0.3 | Low-speed digital signals |
Twisted pair | 100MHz | 0.15 | RS485/CAN bus |
Shielded twisted pair | 500MHz | 0.08 | EtherCAT/Profinet |
Coaxial cable | 6GHz | 0.05 | Video signals/High-frequency measurements |
(2) Impedance Matching Requirements
Impedance specifications for common communication protocols:
Protocol Standard | Characteristic Impedance (Ω) | Tolerance |
RS485 | 120 | ±10% |
USB 2.0 | 90 | ±15% |
Ethernet | 100 | ±5% |
HDMI | 100 | ±5% |

3. Safety Protection Design
(1) Insulation Material Performance Comparison
Material Type | Temp Rating | Breakdown Strength (kV/mm) | Flexibility |
PVC | 105℃ | 15 | Medium |
XLPE | 150℃ | 25 | Low |
TPE | 90℃ | 12 | High |
PTFE | 260℃ | 50 | Medium |
(2) Overcurrent Protection Recommendations
Recommended fuse selection reference:
Wire Gauge (mm²) | Max Fusing Current (A) | Recommended Fuse Rating (A) |
0.5 | 5 | 3 |
1.0 | 10 | 6 |
1.5 | 16 | 10 |
2.5 | 25 | 16 |
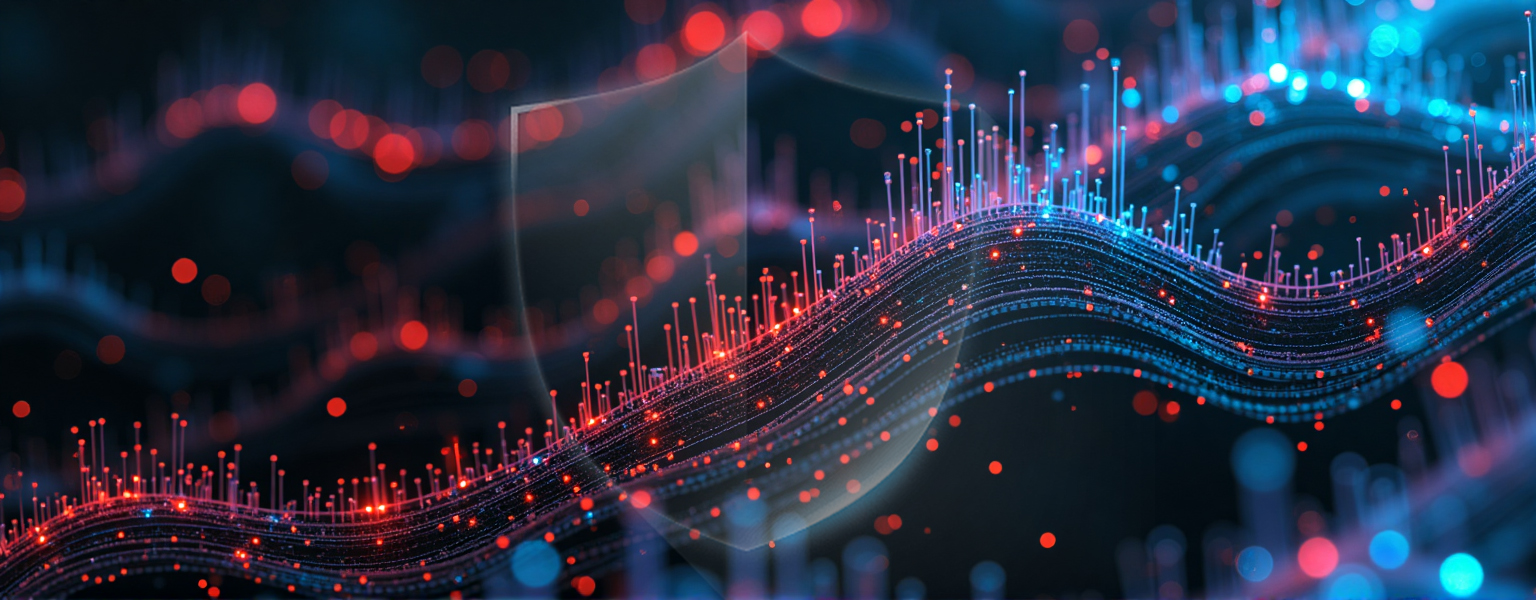
▶ Key Recommendations:
▪Power lines and signal lines must be routed separately with minimum spacing of 3×wire diameter
▪Length variation of high-frequency signal lines should be controlled within ±5%
▪Color coding or permanent labels are recommended to identify different voltage level circuits
II. Mechanical Characteristic Factors
The mechanical characteristics of robot cable harnesses directly affect their reliability and service life in dynamic working environments. The following are key considerations:

1. Motion Performance Parameters
(1) Bending Characteristics Comparison
Parameters | Standard Industrial Cable | Standard Robot Cable | High-Flex Robot Cable |
Minimum Bend Radius | 10×D | 5×D | 3×D |
Bend Life (cycles) | 50,000 | 500,000 | 1,000,000+ |
Allowable Twist Angle | ±90°/m | ±180°/m | ±360°/m |
Axial Tensile Strength (N) | 50 | 100 | 150 |
▶ Note: D represents cable outer diameter
(2) Typical Application Scenarios
▪SCARA Robots: Requires ±180°/m twist tolerance
▪6-Axis Articulated Arms: Requires minimum 3×D bend radius
▪Gantry Robots: Focuses on tensile resistance (>100N)

2. Structural Protection Design
(1) Sheath Material Selection Guide
Material | Wear Resistance | Oil Resistance | Flexibility | Temp Range | Suitable Environment |
PVC | ★★☆ | ★★☆ | ★★★ | -20~80℃ | General indoor |
PUR | ★★★ | ★★★ | ★★☆ | -40~90℃ | Oily environments |
TPE | ★★☆ | ★★☆ | ★★★ | -50~105℃ | Low-temperature |
FEP | ★☆☆ | ★★★ | ★☆☆ | -200~200℃ | High-temperature |
(2) Compression Resistance Requirements
▪Conventional: Withstands 50N/cm² pressure
▪Cable Carrier: Must pass 100N/cm² test
▪Heavy-duty: Should reach 150N/cm²

3. Installation Method Impact
(1) Mechanical Requirements by Installation
Installation Method | Key Requirements | Typical Lifecycle |
Fixed | Vibration-resistant design | 10+ years |
Cable Carrier | Low-friction jacket + anti-twist structure | 3 million cycles |
Suspended | High-strength tensile braid | 5 years |
Rotary Joint | Special anti-twist layered design | 1 million rotations |

▶ Design Recommendations:
▪Multi-axis robots should adopt “serpentine routing” with 10-15% length margin
▪High-frequency motion areas require dedicated stress relief kits
▪Harness fixing intervals should not exceed 300mm (dynamic) or 500mm (static)
4. Special Mechanical Protection
(1) Impact Resistance Rating
Protection Rating | Test Condition (Impact Energy) | Applicable Standard |
IK06 | 0.5J | General industrial |
IK08 | 2J | Material handling robots |
IK10 | 3J | Construction machinery |
(2) Rodent Protection Design
▪Add anti-chew additives (e.g., capsaicin)
▪Use metal braided shielding
▪Critical circuits should use rigid conduits

▶ Typical Case:
Automotive welding robot harnesses typically require:
▪High-temp PUR jacket (90℃)
▪5 million bend cycle certification
▪Weld spatter resistance design
▪IP67 rated connectors
Selection should involve providing robot motion trajectory and speed parameters to suppliers for professional simulation analysis.
III. Environmental Adaptability Factors
The environmental adaptability of robot cable harnesses directly affects their reliability and lifespan under various working conditions. Here are the key considerations:
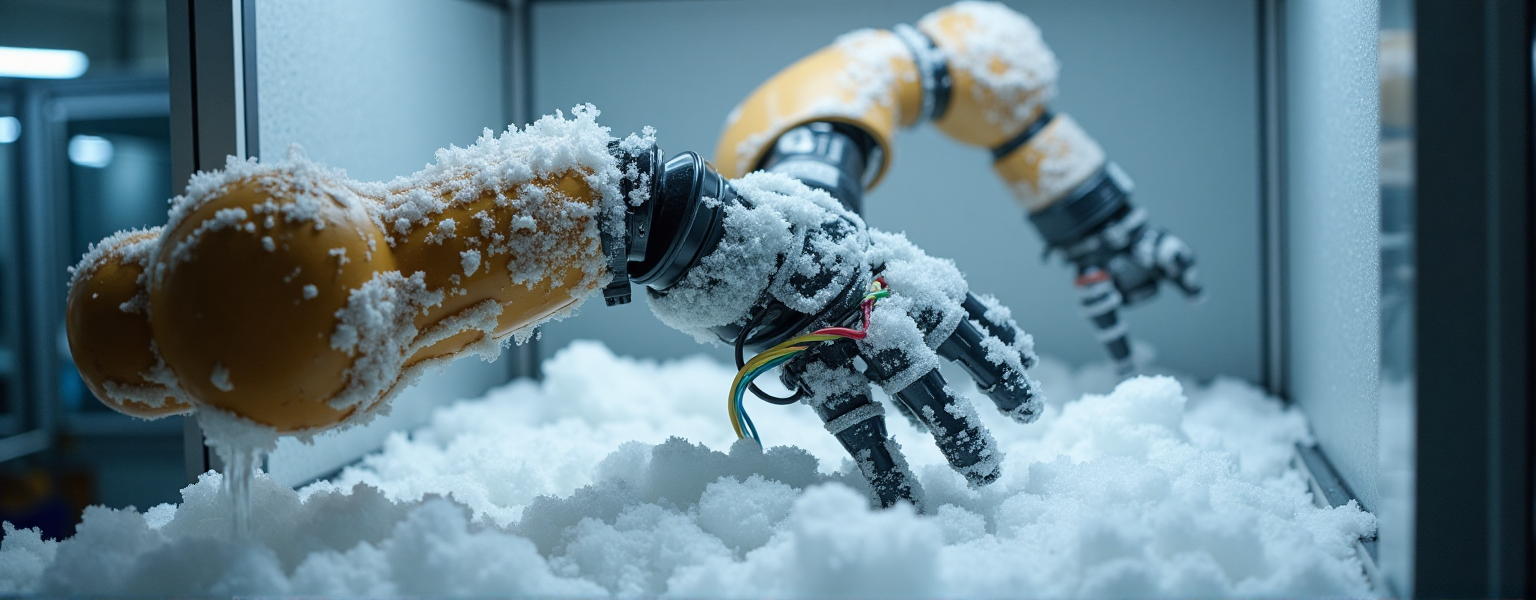
1. Temperature Tolerance
(1) Material Selection for Different Temperature Grades
Temperature Range | Suitable Materials | Typical Applications |
-40℃ ~ +90℃ | Standard PVC/PUR | General industrial environments |
-60℃ ~ +150℃ | Silicone rubber/Special TPE | Automotive welding/foundry workshops |
-200℃ ~ +260℃ | PTFE/FEP | Aerospace/Ultra-low temperature labs |
Above +260℃ | Ceramic fiber/Mica insulation | High-temperature furnaces/Engine compartments |
(2) Temperature Shock Test Requirements
▪Industrial grade: -25℃~85℃ cyclic test 100 times
▪Automotive grade: -40℃~125℃ cyclic test 500 times
▪Military grade: -55℃~150℃ cyclic test 1000 times
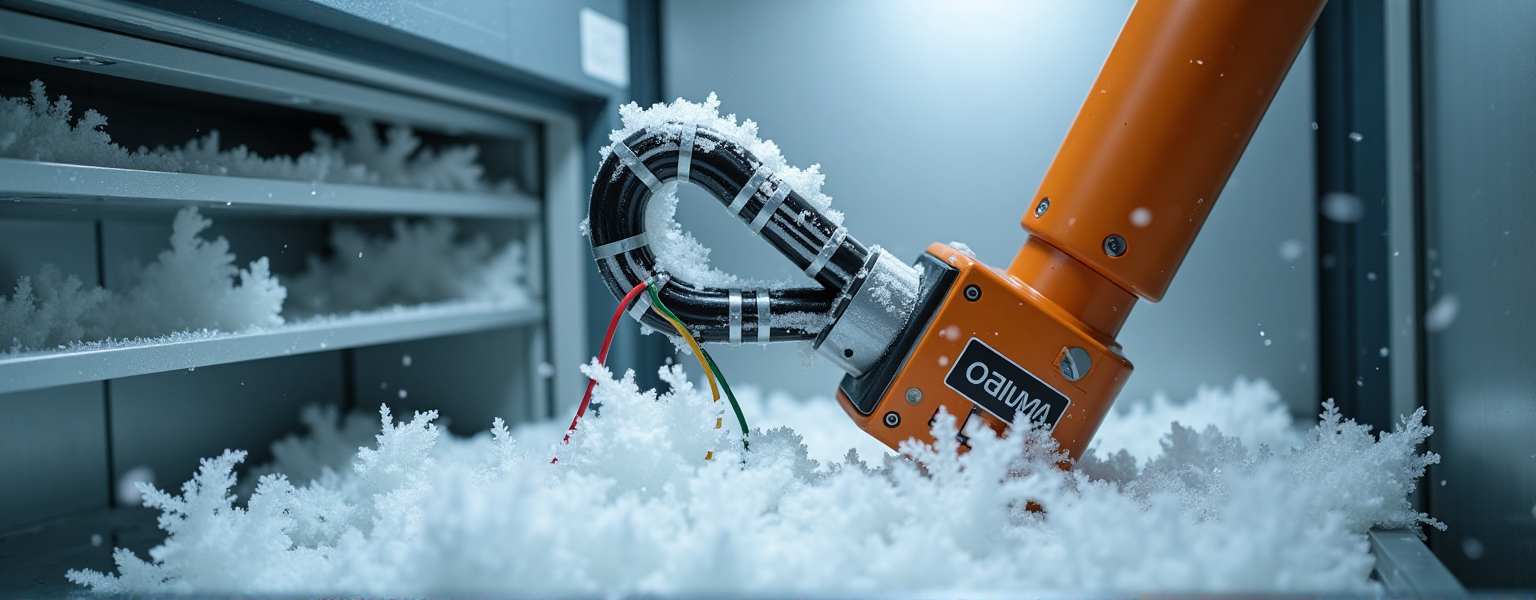
2. Protection Level Selection
(1) IP Protection Rating Comparison Table
IP Rating | Dust Protection | Water Protection | Suitable Environment |
IP54 | Limited dust protection | Splash-proof | Ordinary workshops |
IP65 | Complete dust protection | Low-pressure water jet protection | Food processing/Outdoor |
IP67 | Complete dust protection | Temporary immersion (1m/30min) | Cleaning areas/Construction machinery |
IP69K | Complete dust protection | High-pressure high-temperature water jet protection | Pharmaceutical/High-pressure cleaning |
(2) Special Protection Requirements
▪Salt spray resistance: Coastal areas require 96-hour salt spray test
▪Mold resistance: Humid environments require antibacterial additives
▪Radiation protection: Nuclear facilities require lead shielding

3. Chemical Corrosion Resistance
(1) Chemical Resistance Comparison
Chemical | PVC Resistance | PUR Resistance | PTFE Resistance |
Engine oil | ★★☆ | ★★★ | ★★★ |
Acid/alkali solutions | ★☆☆ | ★★☆ | ★★★ |
Alcohol | ★★☆ | ★★★ | ★★★ |
Hydraulic oil | ★☆☆ | ★★★ | ★★★ |
(2) Certification Requirements
▪Food grade: Complies with FDA 21 CFR or EU 10/2011
▪Medical grade: Meets USP Class VI biocompatibility
▪Automotive grade: Passes SAE J1128 fuel resistance test

4. Special Environment Applications
(1) Extreme Environment Solutions
Environment Type | Solution | Key Indicator |
High altitude | Increased insulation thickness | Corona resistance >5000m |
Strong EMI | Double shielding + ferrite filter | Shielding effectiveness >90dB |
Vacuum environment | Non-outgassing materials | Outgassing rate <1% TML |
Explosive environment | Intrinsically safe design | ATEX/IECEx certified |
▶ Design Recommendations:
▪For multi-environment scenarios, adopt the “highest standard” principle
▪Chemical environments recommend fully sealed connectors + potting process
▪Outdoor applications require UV protection layer (e.g. carbon black additive)
5. Vibration and Shock
(1) Vibration Level Requirements
Application | Vibration Frequency | Acceleration | Test Standard |
Fixed installation | 10-50Hz | 1g | IEC 60068-2-6 |
Mobile robots | 5-200Hz | 3g | ISO 16750-3 |
Construction machinery | 5-500Hz | 5g | SAE J2380 |
▶ Typical Case:
Semiconductor cleanroom robot harnesses typically require:
▪Silicon-free and dust-free materials
▪Passes Class 100 cleanliness test
▪Anti-static design (surface resistance 10^6-10^9Ω)
▪White appearance for particle detection
IV. Connector and Interface Factors
As a critical component of robot cable harnesses, connectors directly affect system reliability and maintenance convenience. Below is a detailed selection guide:

1. Connector Type Selection
(1) Comparison of Common Industrial Connectors
Type | Typical Spec | Contact Count | Protection Rating | Application | Mating Cycles |
M8 | 3/4/5-pin | 3-8 | IP67 | Sensors | 500 |
M12 | 3/4/5/8-pin | 3-12 | IP68 | I/O Devices | 1000 |
7/8″ | 6-19-pin | 6-19 | IP69K | Servo Motors | 5000 |
Han | 6-96-pin | 6-96 | IP65 | Power Distribution | 2500 |
(2) Special Function Connectors
▪Hybrid: Integrates power+signal+fiber (e.g. HARTING Han-Modular)
▪High-frequency: Supports 10Gbps transmission (e.g. RJ45 Cat6A)
▪High-temp resistant: Ceramic material (operating temp >200℃)
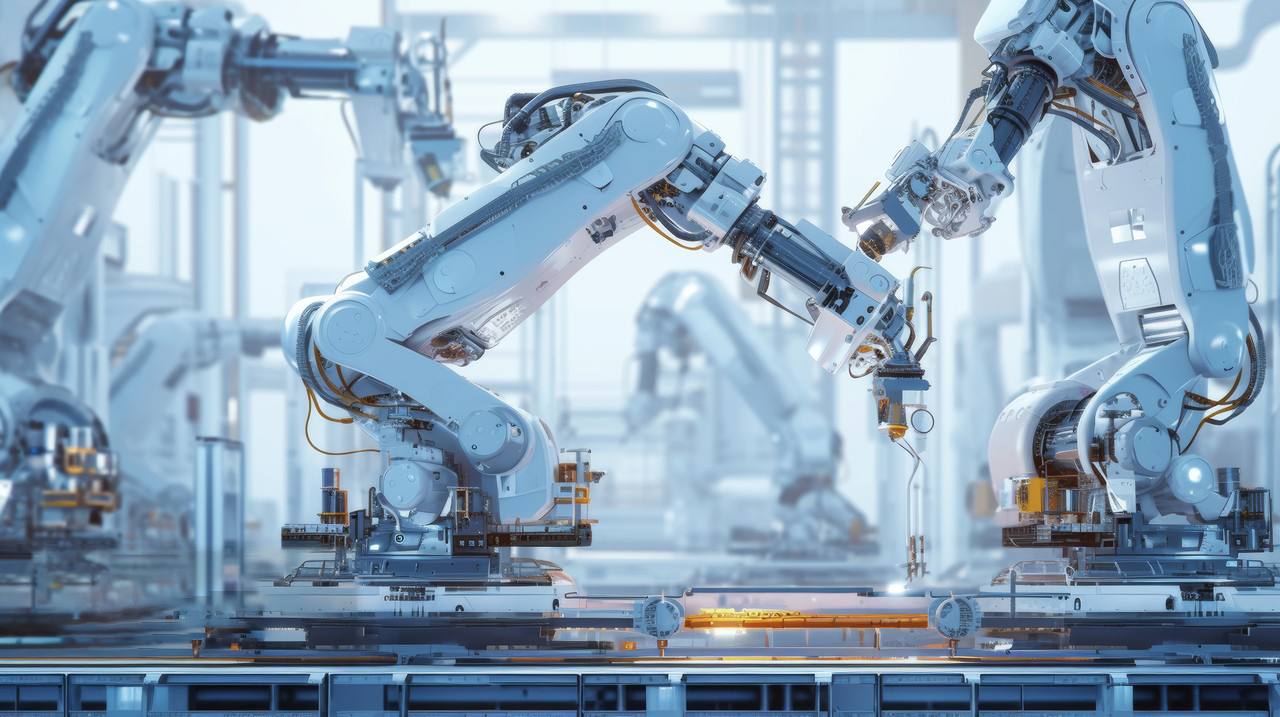
2. Interface Performance Parameters
(1) Electrical Characteristics
Parameter | Signal | Power | Hybrid |
Rated Voltage | 60V | 600V | 300V |
Rated Current | 2A/contact | 40A/contact | 10A/contact |
Contact Resistance | <20mΩ | <5mΩ | <10mΩ |
Insulation Resistance | >1000MΩ | >5000MΩ | >3000MΩ |
(2) Mechanical Performance
▪Mating Force: 3-20N(signal)/20-80N(power)
▪Retention Force: >50N(prevent accidental disconnection)
▪Vibration Resistance: 5-2000Hz, 15g acceleration
3. Termination Technology
(1) Termination Methods Comparison
Method | Tools | Reliability | Wire Size | Difficulty |
Crimp | Special tool | ★★★ | 0.08-6mm² | ★★☆ |
Solder | Soldering station | ★★☆ | 0.05-2.5mm² | ★★★ |
Spring | None | ★★☆ | 0.14-4mm² | ★☆☆ |
IDC | Punch-down tool | ★★☆ | 0.1-0.5mm² | ★★☆ |
(2) Termination Recommendations
▪Power: Crimp + heat shrink preferred
▪Signal: Gold-plated contacts + spot welding
▪High-frequency: Impedance-matched termination
4. Protection and Maintenance Design
(1) Protection Enhancement
Challenge | Solution | Effect |
Dust | Sealing ring + gasket | IP6X |
Liquid | Dual-seal structure | IPX8 |
Oil | Oil-resistant rubber | Oil-proof |
EMC | Metal housing + filter | 30dB shielding |
(2) Maintenance-friendly Features
▪Color coding: Different colors for voltage levels
▪Quick-connect: Tool-free mating
▪Status LED: Power indicator
▪Keying: Prevents mis-mating

▶ Selection Guidelines:
▪Prioritize 360° rotatable connectors for multi-axis robots
▪Choose locking mechanism models for vibration environments
▪Recommend modular connector systems for high-density wiring
▪Reserve 10% spare contacts for critical positions
▶ Typical Case:
Automotive welding robot connector configuration:
▪Power: 7/8″ 12-pin (IP67)
▪Signal: M12 5-pin D-coded (IP68)
▪Network: M12 X-coded (IP69K)
▪All with gold-plated contacts + secondary locking
V. Standards and Certification Factors
Standards and certifications are crucial guarantees for ensuring the quality, safety and compliance of robot cable harnesses. Below is a detailed analysis of certification requirements:
1. Basic Safety Certifications
(1) Comparison of Global Safety Certifications
Certification | Region | Key Tests | Validity | Logo |
UL | North America | Fire resistance | Annual audit | ![UL] |
CE | EU | EMC + Safety | Self-declaration | ![CE] |
CCC | China | Safety performance | Annual audit | ![CCC] |
PSE | Japan | Electrical safety | 3-7 years | ![PSE] |
▶ Note: Actual products should display complete certification marks
(2) Key Test Items
▪Withstand Voltage Test: AC 1500V/1min no breakdown
▪Insulation Resistance: ≥100MΩ(500VDC)
▪Flammability Test: UL94 V-0 flame retardant
▪Mechanical Strength: 50N pull test
2. Industry-Specific Standards
(1) Core Standards by Industry
Industry | Main Standards | Special Requirements |
Industrial Robots | ISO 10218-1/-2 | EMI immunity ≥20V/m |
Automotive | LV214/ISO 6722 | Oil + high temp resistance (125℃) |
Medical Devices | ISO 13485 | Biocompatibility testing |
Aerospace | AS/EN 9100 | Failure stress ≥3x working load |
Food Processing | FDA 21 CFR/EC 1935/2004 | No migrating harmful substances |
(2) Special Harness Certifications
▪Bend Life Certification: Requires third-party test reports
▪EMC Testing: Includes radiated emissions + immunity tests
▪Environmental Aging: Temperature cycling + damp heat tests
3. Material Compliance
(1) Hazardous Substance Restrictions
Substance | RoHS Limit | REACH Requirements | Test Method |
Lead (Pb) | <1000ppm | SVHC notification | ICP-MS |
Cadmium (Cd) | <100ppm | Banned | Atomic absorption |
Hexavalent Chromium (Cr6+) | <1000ppm | Restricted | Colorimetry |
Phthalates | <1000ppm | Authorization list | GC-MS |
(2) Environmental Certifications
▪Halogen-Free: Chlorine + Bromine <900ppm
▪REACH SVHC: Currently 219 Substances of Very High Concern
▪TUV Eco Certification: Meets Blue Angel standards
4. International Standards Comparison
(1) Wire Gauge Conversion
China(GB) | US(AWG) | International(IEC) | CSA(mm²) |
0.5 | 20 | 0.5 | 0.52 |
1.0 | 18 | 1.0 | 1.04 |
1.5 | 16 | 1.5 | 1.56 |
2.5 | 14 | 2.5 | 2.63 |
(2) Test Standard Equivalents
Withstand Voltage:
▪IEC 60335-1: 1250V
▪UL 758: 1500V
▪GB 5023: 2000V
5. Certification Implementation
Procurement Checklist:
▪Require valid certification documents from suppliers
▪Verify test reports match product models
▪Critical components (e.g. connectors) need separate certification
▪Conduct regular factory audits (especially for UL)
Typical Case:
Automotive robot harness certifications:
▪Electrical Safety: UL 758 + LV214
▪Environmental: ISO 16750-4
▪Material Compliance: IMDS Report
▪EMC: CISPR 25 Class 3
Special Notes:
▪Export products must comply with destination country’s latest regulations
▪Medical/food industry certification typically takes 6-12 months
▪Aerospace certification costs may be 5-10x industrial products
▶ A complete standards system ensures harness reliability in:
▪Long-term safety
▪Equipment compatibility
▪Special environment adaptability
▪Global market access

No comments to show.
Leave a Comment